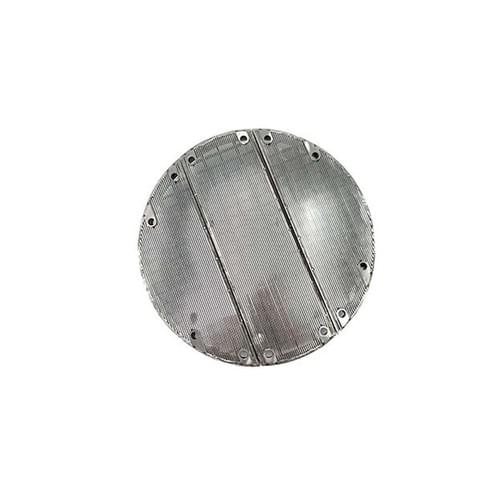
Catalyst Support Grid
Catalyst Support Grid for Reactors
A catalyst support grid is a critical component in reactor systems, providing stable and durable support for catalysts during chemical processes. The structure is composed of support girders—typically T-type or I-type—along with the catalyst support grid itself and an upper layer of V-wire wrapped screens.
The support girders rest securely on the bosses of the reactor walls, ensuring a solid foundation. The grid is then placed on top of these girders and bosses, creating a stable platform. To enhance durability and functionality, a V-wire screen or two layers of thick and thin stainless steel mesh are welded onto the grid. This ensures strength and proper filtration while preventing damage or clogging from catalyst particles.
The upper part of the grid is designed to hold magnetic balls and catalysts, ensuring that the process flows smoothly with even distribution. The V-wire wrapped screen offers optimal filtration while allowing for the smooth passage of process fluids, preventing clogging or pressure build-up.
With this carefully engineered structure, catalyst support grids provide the strength, stability, and filtration needed for efficient reactor operation, ensuring long-lasting performance and minimizing maintenance needs.
Catalyst Support Grid for High-Temperature Reactor Applications
The catalyst support grid and girder play a crucial role in reactor operations, particularly in high-temperature and corrosive environments. These components must have high strength and rigidity to withstand extreme conditions. Not only should the structure resist bending and deformation at high temperatures, but it must also offer corrosion resistance, making stainless steel the preferred material for girders, grids, and wire mesh construction.
Design Considerations:
When designing the catalyst support grid, factors such as the weight of the catalyst and magnetic balls, the self-weight of the support plate, the bed pressure drop, and the operating liquid load are carefully taken into account. These parameters are used to calculate the structural dimensions of the support beam and grid, ensuring the grid can perform reliably in demanding environments.
Key Features:
1. High Strength:
As one of the earliest manufacturers of wedge wire screens in China, we have extensive experience and advanced production technology. Our welding processes, developed over years of research and refinement, ensure our products meet the highest industry standards. Even in hydrocracking and desulfurization reactors, where the catalyst support grid must withstand loads of 350 kPa or more, our grids resist collapse or bending, ensuring reliable operation.
2. Precise Slot Sizes:
Our wedge wire screens feature accurate gap (slot) sizes, with a minimum slot size of 10 microns, allowing them to reliably retain fine catalysts, resins, or molecular sieves. The continuous slotting structure of wedge wire screens provides a higher open area compared to other wire mesh products, ensuring efficient flow even with small gaps.
3. Special Surface Treatment:
We use an environmentally friendly surface treatment process that goes beyond traditional pickling. This method creates a smoother surface on the final product, reducing material wear on the screen and enhancing the screen’s durability. The smoother surface also enhances corrosion resistanc, increasing the lifespan of the grid.
4. Detachable Structure:
Our grids are designed with a detachable structure, making them easy to assemble and disassemble. This allows for customized solutions tailored to meet specific customer needs, facilitating maintenance and future expansions.
5. Automatic Cleaning & High Efficiency:
The smooth surface of the screen also supports automatic cleaning, reducing maintenance needs and ensuring high screening efficiency. The design not only increases the product’s anti-corrosion capabilities but also extends its service life in harsh operating conditions.
Our catalyst support grids are engineered to deliver exceptional performance in demanding reactor environments, offering durability, precision, and efficiency. With our custom design and manufacturing capabilities, we meet the specific needs of each customer, providing reliable and long-lasting solutions for critical reactor applications.